The news of the Novo Nordisk (Novo Holdings) intent to acquire Catalent has taken the…
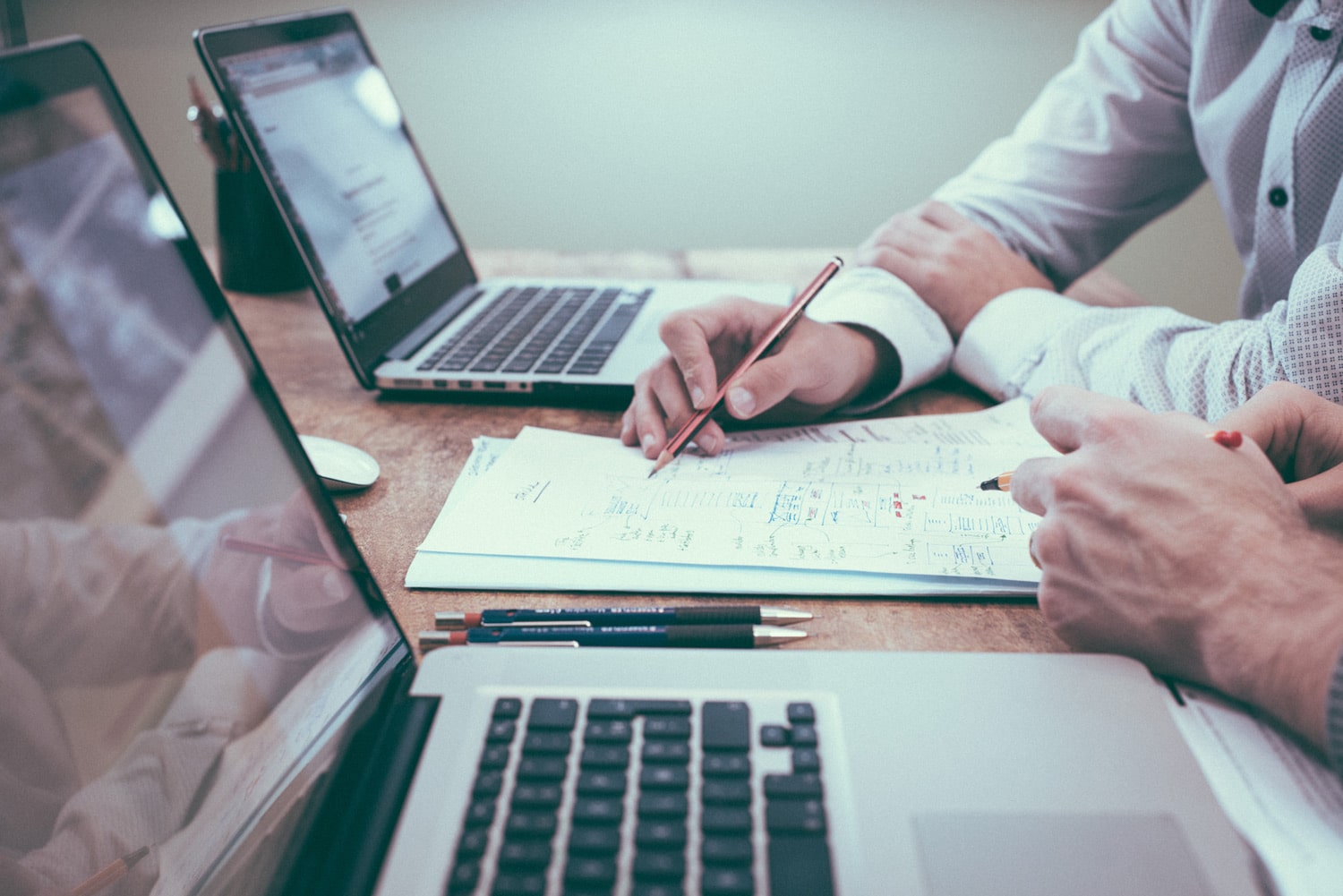
Audit Readiness Checklist
Sooner or later, every biotech, pharma or medical device company will face an audit. Use this general checklist to evaluate your organization and take proactive steps to prepare to pass an audit when the time comes.
Management Responsibility and Quality System
[Y/N] — Are your organization’s Quality Policy and Quality Objectives documented?
[Y/N] — Does your organization have a Quality Manual documenting the quality system and its implementation?
[Y/N] — Is the Quality function separate from the Production function?
[Y/N] — Are quality procedures and responsibilities documented?
[Y/N] — Does QA have the authority for all quality matters?
[Y/N] — Is the suitability and the effectiveness of the quality system reviewed by management at defined intervals?
[Y/N] — Does your organization have a documented plan for recovery and return to operations following a disaster?
[Y/N] — Does your organization have written procedures for handling customer complaints?
[Y/N] — Do procedures ensure that root causes of customer complaints are investigated and resolved, and effectiveness of corrective and preventative actions are verified?
Documentation and Records
[Y/N] — Are procedures available for the control of documents and records?
[Y/N] — Do these procedures address the handling of document changes?
[Y/N] — Are there written manufacturing or service instructions?
[Y/N] — Is there a process for the approval of procedures/service instructions?
[Y/N] — Is there a system for record retention?
[Y/N] — Are records retained in accordance with the applicable regulatory requirements?
Facilities
Infrastructure — Are the requirements defined for the infrastructure needed to:
[Y/N] — Achieve conformity to product requirements
[Y/N] — Prevent product mix-up and
[Y/N] — Ensure orderly handling of product
[Y/N] — Is there a security system to assure there is no entry by unauthorized persons?
[Y/N] — Is there a written preventative maintenance program for all equipment and critical utilities?
[Y/N] —Is there a pest control program including approved insecticides and areas applied?
Equipment
[Y/N] — Are manufacturing and lab equipment and critical utilities qualified according to the written protocols and industry standards?
[Y/N] — Is equipment maintained and calibrated according to a preventive maintenance schedule?
[Y/N] — Are the calibration maintenance intervals based on the manufacturer’s specified frequencies?
[Y/N] — Are records maintained for maintenance and calibration operations?
[Y/N] — Are there written procedures for cleaning, specifying cleaning agents and methods?
[Y/N] — Is there data and cleaning validation reports to show that the residuals left by the cleaning and/or sanitizing agent are within acceptable limits when cleaning is performed in accordance with the approved method?
[Y/N] — Is there an adequate system to assure that unclean instruments, equipment and machines are not used?
[Y/N] — Is there proper storage of cleaned instruments and equipment so as to prevent contamination?
[Y/N] — Is there an adequate system for controlling changes to methods, documents related to equipment, machines?
[Y/N] — Are changes authorized and approved through quality?
[Y/N] — Is re-qualification or re-validation performed post any major changes to the equipment and/or machine?
Purchasing Controls and Materials
[Y/N] — Is there a system in place to ensure that materials are only purchased from approved suppliers?
[Y/N] — Has each supplier of material or component been inspected, evaluated or audited for proper manufacturing controls?
[Y/N] — Are batch records used to document the material, equipment, machine and process(es) used in the production?
[Y/N] — Are there written procedures for the receipt, testing and release for use of all materials?
[Y/N] — Are incoming materials inspected?
[Y/N] — Are incoming material/components quarantined until approved for use?
[Y/N] — Are rejected components, material and containers quarantined and clearly marked to prevent their use?
[Y/N] — Is there a segregated area for non-conforming product?
[Y/N] — Is a final inspection performed on the completed product?
[Y/N] — Is there a system for handling non-conforming product materials or test results to prevent reoccurrence?
[Y/N] — Is each lot within each shipment of material or components assigned a distinctive code so material or components can be traced through manufacturing and distribution?
Production
[Y/N] — Have any of your manufacturing processes been validated?
[Y/N] — Does your facility have design control for any products manufactured?
[Y/N] — Are planned and unplanned deviations documented?
[Y/N] — Is there a procedure for the documentation and investigation of non-conformances?
[Y/N] — Is production data reviewed for potential trends in non-conforming product?
[Y/N] — Are adverse trends addressed and is appropriate management notified?
[Y/N] — Does your firm subcontract the assembly and/or packaging of the product?
Laboratory Controls
[Y/N] — Do you have an on-site laboratory to test incoming materials and finished product?
[Y/N] — Is there a procedure for investigation of out-of-specification (OOS) test results to assure that a uniform procedure is followed to determine why the OOS result occurred and that corrective actions are implemented?
[Y/N] — Are non-conformances tracked and trended?
[Y/N] — Are all your contract labs/manufacturers qualified?
[Y/N] — Do your contract labs/suppliers follow current good manufacturing practice /good laboratory practice requirements?
[Y/N] — Is there a written specification on how to qualify contract labs/manufacturers?
Field Actions/Recalls
[Y/N] — Have any field alerts, recalls or market withdrawals been issued, are procedures in place?
Change Control / Notification
[Y/N] — Is there a system in place to manage process changes? If yes, is this process detailed in a written procedure?
[Y/N] — Do you routinely notify customers of changes that potentially affect the quality of the product or service provided?
[Y/N] — Do you routinely notify customers of key business changes (e.g. acquisitions, manufacturing location changes, etc.)?
[Y/N] — Do you notify customers in advance of significant changes to processes/materials? What is the notification process?
Corrective and Preventive Action
[Y/N] — Are procedures in place for Corrective and Preventive Action?
[Y/N] — Are corrective and preventive actions assigned and tracked to closure?
[Y/N] — Are records maintained for corrective and preventive actions?
[Y/N] — Are corrective and preventive actions reviewed for effectiveness?
[Y/N] — Are corrective actions periodically reviewed by top management?
Internal Audits/Supplier Management
[Y/N] — Is there a documented internal audit program in place at your organization?
[Y/N] — Are internal audits performed on a schedule and corrective actions taken as appropriate?
[Y/N] — Are internal audits periodically reviewed by top management?
[Y/N] — Does your organization maintain an approved supplier list?
[Y/N] — Does your organization have a procedure/process outlining the selection and monitoring of suppliers providing critical products and/or services?
Training
Are trainings conducted?
[Y/N] — Internal QMS training
[Y/N] — Job specific training
[Y/N] — Are employee training records maintained in compliance with Control of Records?
[Y/N] — Are personnel qualifications, skills in accordance with the job performed and job descriptions available?